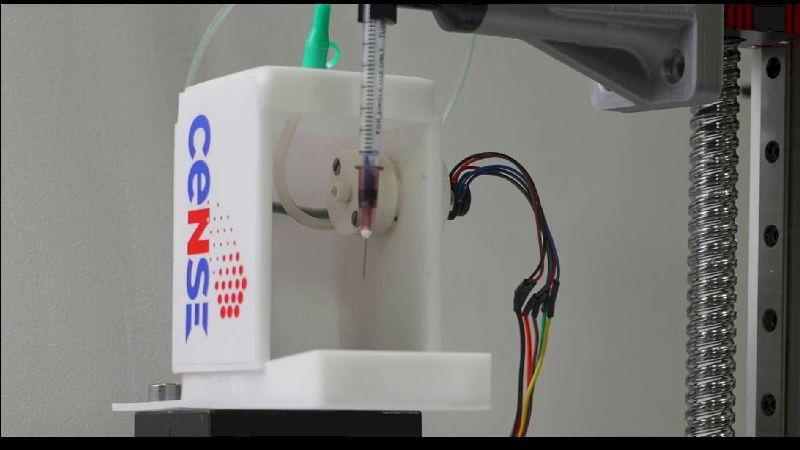
Novel printing setup designed by researchers at IISc. Image credits: MDHS Lab,CeNSE
We routinely use the technology of printing to manufacture electronic circuits, in inkjet printers to produce colourful images and texts, and even to 3D-print automobile components. Moreover, bioprinting — making tissues and organs from biological material — has become an emerging area of medical research in recent years. But, most printing techniques are suited for very specific applications and cannot handle a variety of printing materials. For some biological testing applications, liquids suspended with proteins, polymers and large biological cells need to be printed on chips or glass slides, which would clog conventional inkjet printers.
Newer techniques that print such liquids use lasers and electric fields, making the process complex and expensive. As a cheaper alternative, researchers at the Indian Institute of Science (IISc), Bengaluru, have developed a new technique that can effectively print a wide range of liquids inks including biopolymers, biological solutions containing cells, as well as water-based inks. The study, funded by the Department of Science and Technology (DST) and the Ministry of Electronics and Information Technology, Government of India, was published in the journal Nature Communications.
The novel setup consists of a pump that drops liquid ink from the desired height onto a copper mesh having micrometre-sized pores. As the ink passes through the mesh, it turns into tiny droplets that fall at precise locations on a chosen material, such as a glass slide, producing the required pattern. Through previous techniques, scientists could only create ink droplets of a fixed size as it is not easy to change the size of the printing nozzle. The mesh used in the current technique allows them to generate droplets with a wide range of sizes — from a few tens of micrometres to about a millimetre.
“Our setup is simple to handle. We can easily replace the meshes while printing and change the pore sizes,” says Chandantaru Dey Modak, a PhD scholar at IISc and the first author of the study.
The mesh provides other advantages too. The researchers chemically treated the copper meshes to make them ‘superhydrophobic’, that is, extremely repulsive to water. This property helped in creating cleaner prints since they could pass a single droplet of ink at a time through a pore, thus avoiding ink spots due to unwanted extra droplets.
“The use of a mesh makes this technique very cost-effective. One mesh costs around $9 when compared to an ink cartridge, used in nozzle-based techniques, that is around $200 to $300,” adds Chandantaru.
The researchers were able to print with thicker inks having a large number of suspended particles. Their setup allowed them to increase the concentration of suspended particles to 71% from 41% achievable through nozzle-based techniques.
“We could easily print large biological cells, which was not possible earlier because the nozzles used to clog,” says Chandantaru. In a nozzle, which always has some ink passing through it, the solvent in the ink evaporates over time, and the suspended particles clog the nozzle opening. On the other hand, the liquid ink is dropped onto the mesh only when printing, giving the particles very little time to jam it. Moreover, cleaning the mesh is easier. The researchers found no clogging even when the ink contained particles as large as one-fourth the size of the pore.
The researchers demonstrated various applications of the technique in addition to printing biological samples. They printed electrical conducting lines used in circuit boards and also made a tiny, working diode — a device found in LEDs, solar panels and voltage regulators. They also created small micron-sized 3D pillars with their setup, indicating the possibility of printing at the micron-scale.
A limitation of the existing printing techniques, including this one, is that they cannot print highly viscous liquids such as hydrogel that is used in bio-inks for printing artificial live tissues.
“Viscous liquids don’t flow easily. So our pump would have to eject such liquids with a higher force. But that would generate some extra unwanted liquid droplets, and not give a clean print,” explains Chandantaru.
The researchers, however, are working on removing this limitation. They are also trying to improve their technique with parallelisation — that is, printing different liquids at the same time using a single mesh.
“Parallelisation is useful in bioprinting, where cells are printed followed by a layer of food to grow them, and also in 3-D printing, to print layers of different materials one upon the other,” he adds.
Currently, the researchers are looking for industrial collaborators to make this technique commercially available on a larger scale.
“A future goal will be to do rigorous experiments on biological and electronic printing applications,” signs off Chandantaru.
This article has been run past the researchers, whose work is covered, to ensure accuracy