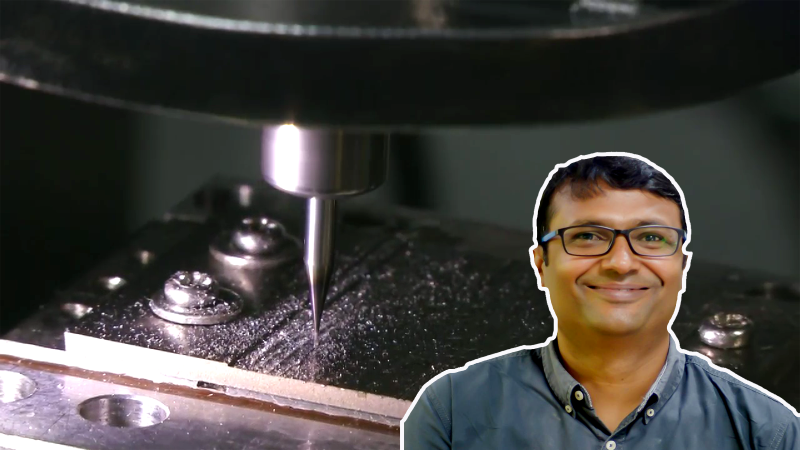
Image: Micromachining tool in action. Inset : Prof. Ramesh Singh. Courtesy IIT Bombay
If you have ever seen an opened wristwatch machine, you would see several tiny parts with intricate shapes and designs. We use miniaturised parts and products frequently, as components of the many machines that we use or jewellery with which we adorn ourselves. Miniature products are also needed in biomedical devices, defence applications and for creating microscale moulds. Making tiny parts calls for very fine manufacturing processes.
The Ultra High-speed Micro Machining Centre, conceived, designed and built in the Machine Tools Lab at the Indian Institute of Technology, Bombay, is a machine that can make high precision micro components. The designers of this system, led by Prof Ramesh Singh, believe that it is one of the most precise machines to be designed and built in India. The Ultra High-speed Micromachining Centre can compete with state-of-art German and Singaporean systems and will boost the global competitiveness of the Indian industry in the micromanufacturing domain.
Machining is one of the most common processes used to manufacture parts. Conventional machining methods include drilling, milling, shaping and sawing. These methods use a sharp tool to remove material from a block to create the desired shape. Material can also be removed using chemical, thermal or electrochemical processes to shape it to the desired part. Methods that remove material to make the desired shape are called ‘subtractive’. This process is contrary to making objects by adding material in a controlled fashion, 3D printing being a recent example.
We can use either subtractive or additive processes to make tiny parts having dimensions in micrometres or microns (1000th of a millimetre). At the microscale, chemical, thermal or electrochemical processes are limited in the shapes they can create and the materials they can process. They are typically used in electronics and on silicon material. In comparison, the mechanical machining processes are more versatile.
Mechanical micromachining can create freeform features in a wide range of materials using traditional machining in the range of 0.1 mm to 5 mm sizes. Making even smaller parts is challenging. Micromachining solutions from German companies are costly, hence are used sparingly in India. In this light, the micromachining setup developed at IIT Bombay provides a quality manufacturing alternative that is affordable and indigenous.
The Challenges in Micromachining
To make a part using machining, relative motion is essential between the cutting tool and the workpiece or the material from which the part is to be created. The shape of the tool and its penetration into the workpiece surface, combined with the relative motion, produce the desired shape or geometry of the resulting work surface. Rotational motion of the tool or the part is used.
The tools used for micromachining can be extremely thin and small, with approximate dimensions about 1/4 of the thickness of human hair. Such a small tool has very low stiffness and is prone to breakages and failures when used in machining.
Cutting force is the resistance of the material against the intrusion of the cutting tool. Larger cutting force tends to damage the tiny tools. Reducing the cutting forces to avoid breakages in tools poses challenges in the machine design as well as actual machining. The researchers from IIT Bombay have addressed this problem by using high rotational speeds because the cutting force reduces as the relative speed of rotation between the tool and the part increases. Vibrations of the tools and the structure pose another challenge. The team is working towards limiting the vibrations.
The Structure of the Micromachining Centre
Image: Courtesy IIT Bombay
The micromachining unit has a main structure made of granite. Granite has good vibration damping capabilities and is very stable. The low thermal expansion and low thermal conductivity of granite impart thermal stability to the main structure. Basic machining operates on three primary axes-referred to as the X, Y and Z stages. The unprecedented accuracy is attributed to the Z-stage, which has a resolution of 5 nanometers. X and Y stages have submicron resolution and micron-level accuracy. The maximum speed of rotation of the spindle of the micromachining centre is 1,50,000 RPM which is much higher than the 3000 RPM speed of the traditional machines. This helps to reduce cutting forces and protect the cutting tool from breakages.
The material of the tool is tungsten carbide. Some of the tools used in this machine are less than 50 microns, almost 1/3 of human hair.
Wide Range of Applications
Image: Courtesy IIT Bombay
The micromachining process has a wide range of applications. The machine can create micro-holes of about 25 to 50 microns on titanium, which is a material used widely in aerospace and biomedical applications, and is extremely difficult to machine. The micromachining unit can create small features in super hard materials too.
Making micro-mould for a microneedle array is another example. This array can be used for making biomedical implants. The machine can also create various complex geometries and channels with application in microfluidics. Microscale masks, required in techniques such as lithography or printing, can be generated with this machining process.
Another application of the process is in watch and jewellery manufacturing. Different kinds of miniaturised jewellery patterns, designs and aesthetic features can be generated on the components using this technology.
In the current times, everything is transitioning towards digitalisation. Micromachining technology can generate microscale QR codes that can be printed on jewellery and ornaments. They can give access to the linked personalised memories in the form of photos, videos or text messages accessible through a web interface.
The first system developed at IIT Bombay has been working over the last ten years, demonstrating its robustness and durability. Recently, two fully functional high-speed machining systems were supplied to IIT Bhilai and BITS Pilani, Hyderabad campus. The researchers are confident that their machine, with widespread applications, will boost the Atmanirbhar Bharat vision.
Editor’s Note: This is part of the special lab stories feature we are bringing to you.