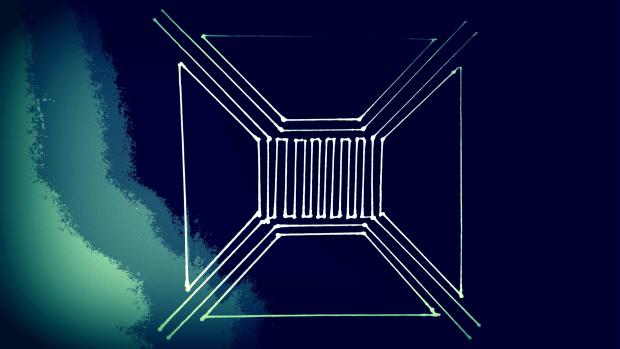
Illustration: Siddharth Kankaria / Research Matters
Over the past few decades, metal oxide semiconductor based gas sensors are gaining attention because they consume less power and respond quicker than conventional gas sensors. However, to deliver their optimal performance, these sensors need to operate at high-temperatures. Microheaters, which are resistive structures on a dielectric membrane whose temperature can be varied by applying an electric current, are used to provide the required high temperatures for the sensors to operate.
Conventionally, microheaters were made up of platinum, polysilicon, or tungsten. Now, a group of scientists led by Prof. Sundarrajan Asokan, from the Department of Instrumentation and Applied Physics, Indian Institute of Science, Bangalore, has fabricated a new type of microheater made of molybdenum that is more durable, stable and consumes lesser power than the conventional ones.
“Temperature uniformity across the microheater surface and stability of the dielectric membrane are the key design criteria of the micro-heaters which are critical in the gas sensing applications. Molybdenum element is perfect for high-temperature applications because of its high melting point and low coefficient of thermal expansion”, says Mr. L.L.Rajeswara Rao, the lead author of the study.
The researchers designed the molybdenum microheaters using a software called ‘CoventorWare’. They also designed a novel technique to fabricate these microheaters on Micro electro-mechanical Systems (MEMS)-based gas sensors. After assessing the electrical, thermal and mechanical characteristics, they found that the molybdenum micro-hotplate integrated with titanium dioxide (TiO2) sensing material could detect carbon monoxide gas at operating temperatures up to 700oC.
For the fabrication, the researchers deposited the molybdenum microheater on a stack of silicon dioxide and silicon nitride membrane. A layer of silicon nitride on the microheater electrically isolated the sensing film from the microheater. Since a low-temperature gradient over the micro heater surface enhances the active surface area of the sensing film and improves the sensitivity of the gas sensor, the researchers achieved a temperature gradient of 9.5oC in the newly developed microheaters.
The researchers also etched out the silicon on which the microheater was placed, to achieve low thermal inertia, thereby decreasing the power consumption and reducing the response and recovery times. The newly designed microheater consumed just 104 mW for a maximum temperature of 800oC and had response and recovery times of 19 and 34 seconds. They also found that the microheater was stable for a continuous operating time of about 600 hours.
When the microheater integrated titanium dioxide MEMS gas sensor was exposed to carbon monoxide (CO) gas, the sensor exhibited the highest response of 84% for 5000 parts per billion (ppb) CO at 500oC and the lower detection limit of the sensor is 500 ppb, confirming that the new sensor is highly suitable for low concentration gas detection at higher operating temperatures.
“The high temperature microheater finds wide applications in the field of micro pellistors, transmission electron microscopy, IR-sources, and detectors”, says Mr. L.L.Rajeswara Rao, who is currently working with GITAM University, Visakhapatnam, now focusing on enhancing the sensitivity of gas sensors using metal additives and nanostructures.