
Batteries play a pivotal role in our modern world, serving as the lifeblood of countless electronic devices ranging from mobile phones to electric vehicles. Their importance in enabling efficient storage, distribution of electricity, and making power available in the absence of grid power supply cannot be overstated. However, batteries are not without their weaknesses, and one of their main vulnerabilities is overheating. Batteries need to be charged, and as they discharge and recharge, they generate heat, compromising their performance.
“All batteries have an optimum temperature at which they work most efficiently. Too much heat can limit battery performance and, in worst scenarios, cause them to catch fire or explode. Lithium-ion batteries, for example, need an optimal temperature range of around 20–40 °Celsius (68–104 °Fahrenheit) to function correctly,” remarks Ekta Singh Shrinet, a doctoral student at Indian Institute of Technology, Bombay (IIT Bombay) and part of a research team that has been studying this phenomenon of battery temperature management.
Ekta is a member of the research team led by Prof. Lalit Kumar in the Department of Energy Science and Engineering at IIT Bombay. In a new study, they now present a novel method to remove heat more uniformly and effectively from the multiple batteries in a battery pack, like those found in electric vehicles, thereby increasing their efficiency and longevity.
“Electric vehicles are a preferred option for dealing with the local environmental problems since they provide a reduction in noise and no harmful gas emissions,” shares Ekta, talking about the motivation for her work.
Electric vehicles use Battery Thermal Management Systems (BTMS) to monitor battery temperatures and maintain the optimum temperatures for the battery to operate. Traditionally, batteries are cooled by circulating a fluid, like water or other liquid coolants, across their surfaces through metal pipes or channels. The area of contact between the coolant and a battery, referred to as the contact area, remains constant. But, as the coolant absorbs heat from each battery in a battery pack, its own temperature keeps increasing, reducing the amount of heat removed from subsequent batteries. To continue removing the same amount of heat from successive batteries then, the contact area has to increase as well.
To overcome the drawback in conventional cooling of batteries, the team led by Prof. Lalit Kumar has come up with a pioneering method to improve the heat transfer. Instead of using a one-size-fits-all method for the coolant carrying channels, they suggested a ‘variable contact area’ method — by adjusting the area where the coolant comes into contact with the battery. They propose increasing this ‘contact area’ along the direction of coolant flow to ensure that the same amount of heat is removed from each battery.
“In our design the contact area between the battery and the coolant increases along the flow direction of the coolant. This means that the area in contact with the coolant gets larger as the coolant moves through the system,” explains Ekta.
With this design, the researchers theorised that the heat would be removed evenly from each battery, maintaining a uniform temperature across the module.
To test their theory, the researchers made a computer simulation of a battery module. The model contained 24 cylindrical lithium-ion batteries, arranged in parallel and packed similar to the ones typically found in an electric vehicle. By simulating various scenarios, where the batteries are put through various charge-discharge cycles, and analysing the results, they noted significant improvements in temperature distribution among the batteries. Their findings indicate a reduction of around 70% in the maximum temperature difference in the different regions within the battery module as compared to conventional methods. Batteries cooled with the proposed system also had a lower maximum temperature.
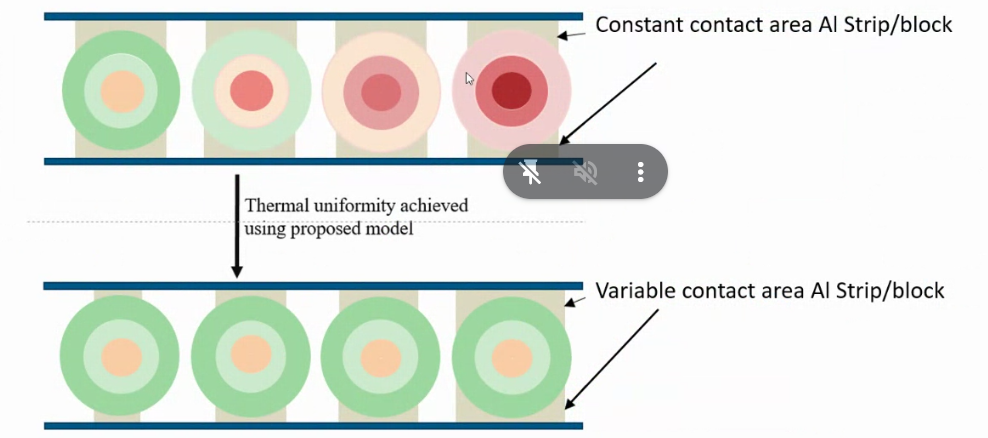
Credit: Ekta Singh Shrinet
Interestingly, the researchers found that batteries in their novel system weigh 57.2 % less than those cooled by the conventional constant contact area method. The weight reduction is due to the reduction in the size of coolant channels in the proposed model, as opposed to the constant size used conventionally. Weight is a significant factor in electric vehicles, because lighter vehicles can travel further before needing a recharge. Since the changes required to achieve this reduction in temperature and weight are minimal, the proposed method does not need any alteration in the electric vehicle manufacturing process.
According to Ekta, “We just need to add or remove a few metal strips to increase or decrease the contact area. This should be a simple change to make in the current manufacturing process”.
The simple change however could improve the performance of an electric vehicle significantly, because of the improved efficiency of the batteries and the reduction in weight.
The researchers believe that their new design strategy will have broad applications not just in the electric vehicle industry, but also solar power storage and other devices which rely on battery packs with multiple batteries. The team has already obtained a patent for their invention. Their work will pave the way for more efficient thermal management systems, contributing to the safety, efficiency and longevity of batteries.