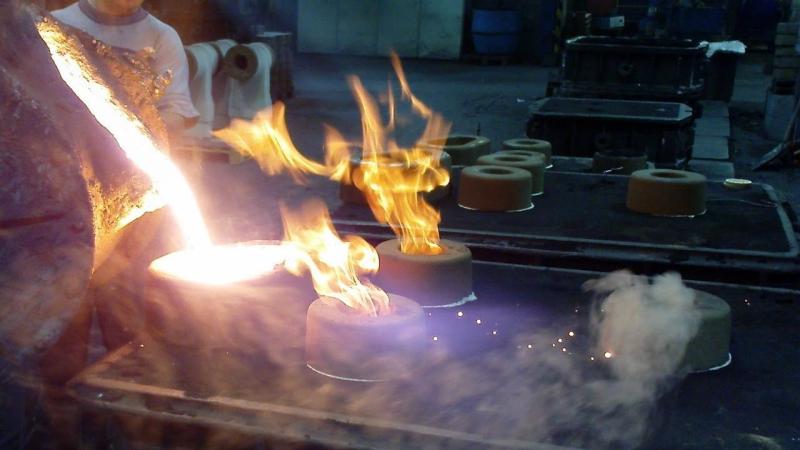
Researchers develop a highly effective solution for recovering green sand in small and medium foundries.
About 70% of the cast metal objects around us, from bathroom taps to automobile gearboxes, are manufactured in foundries using a method called sand casting. Molten metal is poured into moulds made from green sand---a mixture of sand (about 80%) and clay (about 10%). At high temperatures of about 1500℃ required for casting, clay forms a coating on the sand particles, and the sand becomes unusable for further casting. The disposal of such sand has severe environmental and cost implications, particularly for small foundries. In a new study, researchers from the Indian Institute of Technology Bombay (IIT Bombay) have demonstrated a practical and economical way to reuse this green sand.
Although existing methods for reclaiming green sand are capable of processing many tons of sand per hour, they are expensive. Since about 80% of the 4600 foundries in India are of small and medium scale, these methods are unaffordable for them as these foundries can reclaim only about 1000 kg of sand per day. The only viable solution then is to dispose of the green sand by dumping them in water bodies and land. Since used green sand contains heavy metals like lead and tin, which leach into the ground causing water pollution, environmental laws restrict such dumping. On the other hand, buying fresh sand is now expensive since sand mining is banned in most states, further increasing the cost for small and medium scale foundries. Thus, reclaiming used green sand in a cost-effective and scalable approach turns out to be an attractive proposal.
In this study, researchers led by Prof. Sanjay Mahajani of IIT Bombay have proposed mechanical methods to reclaim the sand as opposed to the expensive heat treatment method at 800℃. The team has developed a better, economical and efficient approach to remove the clay using an abrasion and sieving unit.
The key to reclaim the sand is to remove the layer of clay deposited on the sand particles. The team explored various methods to remove the clay deposit mechanically. In the first method the researchers placed the sand in a vertical tube and used a supply of compressed air to enable rubbing of sand particles against each other. In the second case of a horizontal tube is used instead of the vertical tube. This enables additional rubbing of the sand against the walls of the container. Another method made use of small weights to increase the rubbing action or abrasion and a sieve to separate the removed layer of clay. The researchers evaluated the cost and noted the percentage of clay after reclamation for each of the methods.
The researchers found that the best option was the one that used abrasion and sieving. Prof. Mahajani suggested a two stage method where the sand particles are rubbed in the against pebbles in the first stage and sieved in the second stage to separate the clay particles. The sand to be reclaimed is placed in a rotating drum and pebbles of a hard stone such as agate are used for rubbing the clay off the sand particles. The weight of the pebbles needs to be chosen carefully so that clay is removed but the sand particles are not crushed. Pebbles weighing around 40g were found suitable. The second stage uses a rotating drum with a 50 micron (about the thickness of human hair) mesh that acts as a sieve. The sand particles rub against each other in this stage. Since clay particles are smaller in size than sand particles, they pass through the sieve and are collected and disposed of, leaving behind the reusable sand.
In some cases, if the green sand has a substantial moisture content, the efficiency of reclamation is reduced. Hence, the unit has a heater and blower system which first dries the sand before the reclamation process starts.The study found that the rotation speed of the device, the weight and size of agate pebbles, the moisture content of sand and the temperature were some of the factors that can influence the performance of the device.
So how efficient and economical is the proposed new method? The researchers found out that only 2.2% clay remained after the proposed two stage method at the cost of Rs. 550 per ton, while the corresponding numbers were 4.4% at Rs. 2700 per ton for the vertical tube method and 2.2% at Rs. 5600 per ton for the horizontal tube method. Although the setup and installation cost of the proposed two-stage unit is more than other conventional setups, the operating cost is much lower. The process results in a massive 83% savings over buying fresh sand, which costs about Rs 3200 per ton.
The researchers have set up a working prototype of the proposed unit which is capable of processing 100 kg of green sand per hour. "The two-stage device has been installed in the Government Polytechnic College, Kolhapur, Maharashtra", says Prof. Mahajani, talking about the success they have seen so far. "Kolhapur is a large foundry cluster, and many small foundries are operational in this area. We are collecting the waste green sand from small-scale foundries and reclaiming using this prototype. As far as field trial results are concerned, they were found to be satisfactory. They appreciated our work and also started to use our reclaimed sand", he adds.
The study, published in the Journal of Materials Processing Technology, brings in an invention that caters to the needs of small and medium scale foundry owners, who can now abide by the environmental laws and obtain reusable, clean sand with minimal impacts on the environment. The researchers are now improvising on this innovation. "We are working on a hybrid unit which facilitates both thermal and mechanical reclamation. We are also trying to prevent the heat loss as much as possible to reduce the processing cost", shares Prof. Mahajani before signing off.