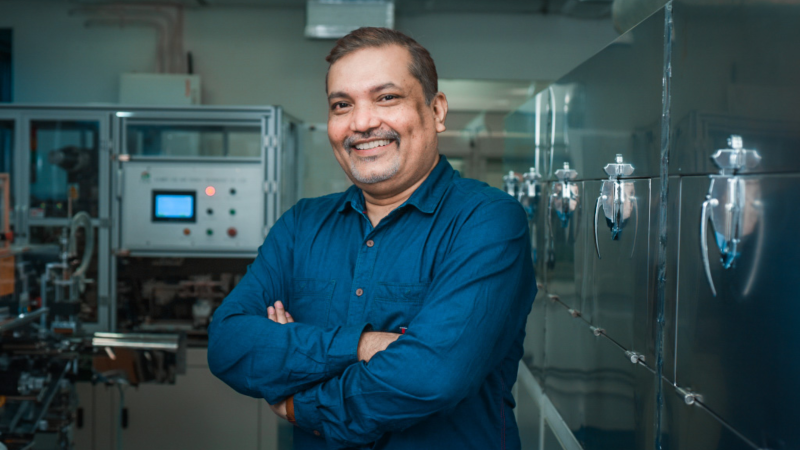
The future of transportation is set to change with the new research and development on electric vehicles. One of the key contributors to this is the energy storage devices—rechargeable batteries. Rechargeable batteries pose numerous challenges and researchers have worked a lot towards addressing those. One of the unique challenges is making safe and efficient storage devices, batteries. Apart from the transportation sector, almost every other industry consuming power will now have to embrace efficient energy storage devices.
Addressing this challenge is the Battery Prototyping Lab at the Indian Institute of Technology Bombay. This is a unique facility that is helping bridge the gap between industry and academia by facilitating the prototyping and scaling up of energy storage technologies. It plays a prominent role in realising the dream of making India self-sufficient in developing and manufacturing energy storage technologies that will meet our unique challenges of the electric mobility and renewable energy sectors. Prof. Sagar Mitra and his team are striving to make a world-class facility to fabricate batteries with a deep know-how of Lithium and sodium-ion battery cell technology. This is located at IITB-Monash Research Academy. The entire project was funded by the Ministry of New and Renewable Energy, Government of India.
The core of a battery is a combination of electrochemical reactions. A battery is composed of mainly three components: cathode, anode and electrolyte. A cathode is the positive pole of a cell that acquires electrons. The anode is the negative or reducing electrode that releases electrons to the external circuit and oxidizes during an electrochemical reaction. An electrolyte is a medium that provides the ion transport mechanism between the cathode and anode of a cell.
Various materials like lithium cobalt oxide (LCO), lithium nickel manganese cobalt oxide (NMC), lithium nickel cobalt oxide doped with alumina (NCA), lithium manganese oxide (LMO), and lithium iron phosphate (LFP) are used as cathode. The anode is usually made of graphite and is the most dangerous material that may catch fire after a full charge and gets dendrite formation during fast charging-discharging. Prof Sagar Mitra and his team at the Electrochemical Energy Laboratory have been working on making batteries safer and they have changed the unsafe components (like graphite) by replacing them with indigenous safe and low-cost materials such as Ferrous Oxide, Silicon and Tin Sulfide, to achieve high energy and a safer battery.
The lithium-ion battery (LIB) is a widely used energy storage technology because it can store more energy per volume and mass (or gravimetric energy density). These batteries are used in portable electronics, electric vehicles and even at power stations to provide an uninterrupted power supply. These batteries have a tiny memory effect (a condition that results in holding a lesser charge), low self-discharge and can be retrieved from deep discharge. In addition, most of the used components are recyclable.
Although LIB has been extensively used, the accessible lithium resources are limited and are not well distributed throughout the world. So, we need an alternative energy storage system that can easily be available and compete with LIB to satisfy our energy/power demand at a lower price. Sodium-ion battery (SIB), one such kind of technology, has been attracting great interest for its low cost. Sodium is abundantly available in the earth’s crust and is distributed fairly uniformly all over the world. For the last few years, our lab has been developing all the three basic components in SIB like cathode, anode and electrolyte to construct a SIB battery cell prototype.
This state-of-the-art facility has equipment like a Power Planetary Vacuum Mixer, Intermittent Coating Machine, Stacking and Winding Machine, Electrolyte Filling Machine and much other sophisticated types of equipment which can convert the raw materials like Lithium, Sodium and Carbon-based powders into functional cylindrical and pouch cells of 2.5 Ah, 7 Ah and 10 Ah capacities. All the critical equipment required for cell fabrication is housed in a state-of-the-art Dry Room, which can maintain a very low relative humidity of 10%, which is as per industry standards.
This facility also has the high-current battery-testing capability through state-of-the-art Battery Cyclers. This Battery Prototyping Lab has a full-fledged production capacity of 4 kWh per day in the format of 10 Ah pouch cells and a capacity of 1 kWh per day in the format of 2.5 Ah 18650 cylindrical cells.
Currently, LiB and NIB in Cylindrical and pouch cells of 2.5Ah, 7Ah, and 10 Ah capacities are made in our facility with 200 Wh/kg energy density of LIBs. For the sodium-ion battery, we are working with KPIT to make cells of 7 Ah pouch capacity with 3000 charge-discharge cycles.
All prototype cells are tested in the field ready to be used in pilot-scale production.
At the moment, they are working on the process development and innovating the electrode design to advance the Lithium-ion battery. This innovation along with the new generation of electrode material will help the Indian cell manufacturing industry in near future. For sodium-ion batteries, this lab is the first in India to make 7 Ah cells with 120 Wh/kg energy density and tested for 3000 cycles, and the industry KPIT is testing the same in 4 kWh pack in 3W applications.
Approximately, ₹ 12,500/kWh is the cost now and expected to bring down the cost under ₹ 9,000/kWh with large quantity pilot-scale production. The lab is also working with several industrial partners to improve performance and cost-effectiveness. Taking a step further, a company named Virya Batteries has been incubated at SINE, IIT Bombay, which has its origins at the Battery Lab at IIT Bombay. Virya Batteries has been a finalist in the National Start-up Awards 2020 organised by the Start-up India program of the Government of India.
The future belongs to sustainable renewable energy generation, like solar and wind. These energy technologies involve considerable storage and discharge, often on demand. Thus, research on rechargeable batteries and their development has become very exciting.
Editor’s Note: This is part of the special lab stories feature we are bringing to you.