
Heat is an inevitable factor in the operation of any computing device, a familiar experience for all who have interacted with laptops, smartphones, or similar gadgets. The prolonged use or engagement in demanding tasks, such as gaming, often exacerbates this issue, leading to significant heat generation. Along with causing inconvenience to the user, this thermal build-up poses various risks to the device, ranging from performance degradation to potential hardware failures.
Every element within an electronic device, be it an integrated circuit, a resistor, or a capacitor, contributes to this thermal output, and necessitates maintaining an ideal operating temperature for optimal functionality. Exceeding this optimal temperature threshold jeopardises not only the individual components but also the overall device performance. Removing any excess heat is paramount to maintaining device performance and longevity.
Conventionally, smaller systems like laptops and mobile devices use small fans that circulate air through the system to remove any excess heat. Larger and more complex systems, like High Performance Computing systems (HPCs) or supercomputers, resort to cooling using liquid coolants and cold plates that dissipate heat. In a recent study, a team of researchers from Indian Institute of Technology, Bombay (IIT Bombay) and Centre for Materials for Electronics Technology (C-MET), Pune have proposed using Low-Temperature Co-fired Ceramic (LTCC) as an efficient alternative to the conventionally used copper for making cold-plates.
In liquid cooled devices, liquid coolants like deionised water (water without any electrical charge) are circulated through the system to remove the excess heat. Cold plates are used like a heat sink transferring the heat from the circuit components into the coolant liquid. Copper is the preferred material for manufacturing cold plates, due to its low cost and high thermal conductivity.
“Copper cold plates are extensively utilised for cooling in HPCs owing to their high thermal conductivity. However, there are limitations associated with copper, such as its weight, susceptibility to corrosion, and challenges in intricate design implementations,'' explains Parikshit Badhe, Senior project associate and a student at the Department of Mechanical Engineering at IIT Bombay who worked under the guidance of Prof. Shankar Krishnan and Prof. Milind Atrey from IIT Bombay.
LTCC is a technology used to manufacture ceramic substrates for circuits. Substrates are materials on which electrical interconnections are printed and other components like resistors, inductors and capacitors are mounted. PCB (Printed circuit boards) is the most commonly used substrate in our daily life electronic devices. LTCC Technology allows compact three-dimensional packing of the circuit, making them smaller and more efficient compared to conventional PCBs. “LTCC technology is already an established manufacturing method for ceramic printed circuit boards. LTCC substrates are extensively used in electronic equipment expected to endure high temperatures, such as automotive and defence equipment,” remarks Parikshit.
This new study demonstrates that microfluidic channels (micrometre sized tiny channels that allow flow of a liquid through it) can be created in an LTCC package to form a cold plate. Thermal testing of these cold plates has shown that they can effectively cool microprocessor chips in supercomputers, successfully restricting temperatures below the safety limits, just as copper cold plates do. This proof-of-concept demonstration is a breakthrough finding that paves the way for integrating cooling solutions directly into the chip package. Essentially, this research validates the concept that if a chip is made using LTCC technology, microfluidic channels can be incorporated into the same package, enabling localised cooling of hot regions by allowing the coolant to penetrate deep into the chip package.
LTCC, though, has a big challenge - its thermal conductivity is poorer (100 times less) compared to copper. This means it is relatively less efficient at conducting heat, which is the key function in cooling systems. The researchers have overcome this hurdle by drilling tiny holes filled with metal, called thermal vias, into the LTCC cooling plate. A team of researchers headed by Dr Shany Joseph from CMET-Pune was instrumental in fabricating these cold plates in their lab.
According to Parikshit “thermal vias are strategically incorporated into the bottom layer of cold plates to facilitate efficient heat transfer from the chip to the coolant via the microchannels embedded within the cold plate”. Owing to the thermal vias, the LTCC's thermal conductivity improved and the thermal resistance dropped by a whopping 43%.
Another challenge of using LTCC cold plates is their tendency for cracking and fracturing.
“LTCC, being a ceramic material, is prone to cracking under uneven tensile loading. To address this issue, a novel clamping mechanism was developed to ensure that the cold plates remain intact without experiencing uneven cracking while fully loading the cold plates on live boards,” says Parikshit.
The team tested the performance of the LTCC cold plates on an Intel® Xeon® Gold 6154 CPU with deionised water as the coolant and compared its performance to that of the copper cold plates. The team also tested two flow patterns - called JI and MC, which determine how the liquid enters and flows through the LTCC cold plates.
“In the MC flow arrangement, the coolant enters from an inlet on one side and exits from the outlet at the other side. In the JI flow arrangement, the fluid enters from the inlet at the centre and leaves from the two outlets at the sides,” explains Parikshit.
While the MC arrangement allows the coolant to flow the entire length of the cold plate, the JI arrangement allows for localised cooling of a hotspot. LTCC cold plates successfully restricted the temperature of the processor below the safety limit at full processor power with both flow patterns.
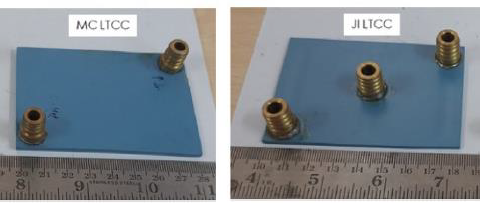
Going forward, the team is looking at further improving the design and functionality of the LTCC cold plates.
“Presently, the designed cold plates are tailored for a 200 W processor range. However, exploring the potential of electroplating at the base of the cold plate to enhance heat spreading can be investigated. This would allow the cold plates to accommodate higher heat inputs effectively,” remarks Prof. Atrey about the future direction of their work.
If commercialised successfully, LTCC-based integrated cold plate technology has the potential to replace conventional cooling systems and chip packaging that are used today. More importantly, demonstrating the use of LTCC cold plates for existing supercomputer chips marks a significant breakthrough in the ongoing research on 3D Integrated Circuits.