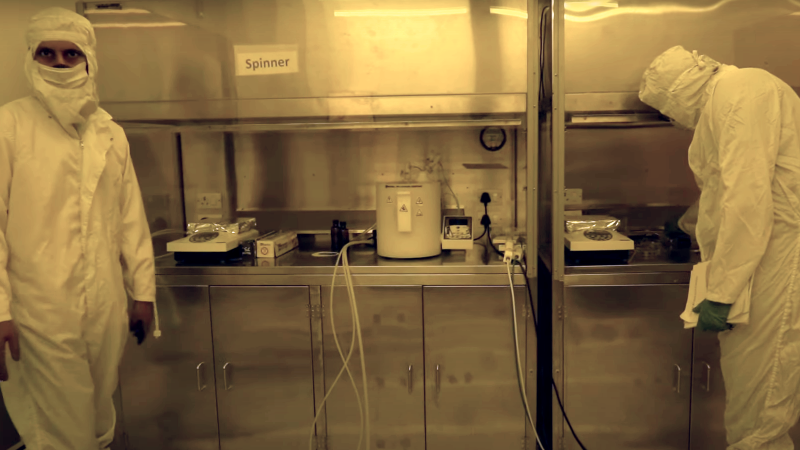
Image Credits: IIT Bombay
Most semiconductor devices are made using silicon as the raw material. Applications such as radar and mobile communication for military and civil applications, signal jamming and RF-charging need semiconductor devices that can operate at high frequencies and high power. Such devices are necessary for commercial space mobile base stations, communication towers, satellite communication, and digital radio. High power RF devices are used in airborne and ship radars and missile seekers in the military space. Especially for military applications, from a security and self-reliance perspective, it is essential to use devices made in India.
Gallium Nitride is a robust material suitable for high power and high-frequency applications. The upcoming Gallium Nitride High Electron Mobility transistor (GaN HEMT) is a promising technology for such applications.
Prof Dipankar Saha and his team at the Indian Institute of Technology Bombay’s Centre for Excellence in Nanoelectronics have worked on making GaN-based solutions. They were the first to make a GaN transistor in India in 2010. They have delivered prototype solutions and undertaken knowledge transfer projects with end-users Bharat Electronics Limited (BEL) and Indian Space Research Organisation (ISRO).
GaN transistors have specific physical properties such as a wide bandgap that allow the devices to carry very high current and switch very fast between on and off state, making them suitable for high power and high-frequency use. When parameters such as maximum operating frequency, and breakdown voltage, among others, are considered, GaN is better than other Silicon, Gallium Arsenide and Silicon Carbide. The GaN semiconductor devices market is valued at USD 977.21 million (INR 74.8 crore) in 2019, and is expected to reach USD 2534.61 million (INR 194.8 core) by 2025. The total RF market is projected to grow to USD 29.27 billion (INR 2241 crores) by 2026.
GaN Device Development at IIT Bombay
Prof Dipankar Saha’s group made the first GaN in 2010 at IIT Bombay. Thereafter it has been over a decade of continuous technology development focusing on RF power applications. The steadfast support of the Ministry of Electronics and Information Technology and the Department of Science and Technology is a key contributing factor to making GaN Technology possible. It has been a story of several years of collaboration with our space agency, ISRO, which takes the IIT Bombay devices, tests them, and gives feedback on their performance. The partnership has led to maturing of the capability to the extent that technology demonstration and knowledge transfer are now underway with a defence company.
The team designs monolithic microwave integrated circuits or MMIC. A monolithic circuit has the entire circuit, including active and passive components, on a single substrate. Active elements, such as transistors, are the ones that need a power supply to function. In contrast, passive components such as resistors and capacitors do not need a power supply to function. Microwave refers to the fact that the operating frequency is in the microwave range of 300MHz to 300GHz.
Let us walk through the process of the design and fabrication of an MMIC on a GaN substrate in the lab at IIT Bombay.
Designing a GaN MMIC
Firstly, the researchers designed a power amplifier using lumped components. This power amplifier has a stability network, a matching network and a biassing network. Then they make a layout from the schematic by replacing each lumped component with an element of the same value from the design library of passive elements—resistors, capacitors and inductors. Then, they make these elements using metal lines on the GaN substrate, after which the components are fabricated.
The GaN power transistor is the central part of designing the active device. The interface design between the alloy, aluminium gallium nitride and the underlying gallium is a crucial part of the design. After the design is done, it is ready to fabricate the circuit.
Fabrication of GaN MMIC
The circuit is fabricated using several sophisticated tools kept in a controlled environment called cleanrooms. The complete MMIC fabrication involves a 9-step patterning process. Electron beam or UV-light can be used to make the patterns, and the processes are called electron beam lithography and photolithography.
The MMIC fabrication process also includes several etching steps, metal deposition, dielectric deposition and annealing. Etching, the removal of unwanted material from specific parts, is carried out in an inductively-coupled plasma-reactive ion etching tool. Metal deposition is done in an Electron Beam evaporator. Annealing is the process of cooling a substance slowly. It is carried out in a rapid thermal annealing tool, where the substrate is quickly heated to a high temperature but is cooled slowly.
A small GaN-based substrate of 2 cm by 1 cm consists of hundreds of HEMT and several MMIC devices. Once the substrate is ready, it is characterised and analysed in the characterisation lab. The GaN devices are very tiny. To see the detailed structure, one needs to observe it under a microscope.
Packaging of the MMIC
The product we get from fabrication is a tiny die, having GaN transistor, capacitors, inductors, resistors, air bridge and transmission lines, all integrated on a single chip to make a power amplifier. The device needs to be packaged to be used on a circuit board.
Microholes are drilled on this die from the backside with a tool called deep reactive ion etching. Then, around 10-micrometre thick gold electroplating is done on the rear of this die to connect ground points on the front side to the bottom ground plane. The die is ready to be mounted on the packaging, including a heat sink and spacer to make an electrical connection from PCB to die. It is mounted on the spacer, and gold wire bonding is done from the spacer leading to the die pad.
The lab can support customising GaN devices for various civilian and strategic applications, thanks to its capabilities to fabricate GaN devices at a fraction of usual licensing costs, making prototype devices and MMICs and being able to facilitate the design of RF power amplifiers using the IIT Bombay fabrication lab or third party commercial fabrication units.