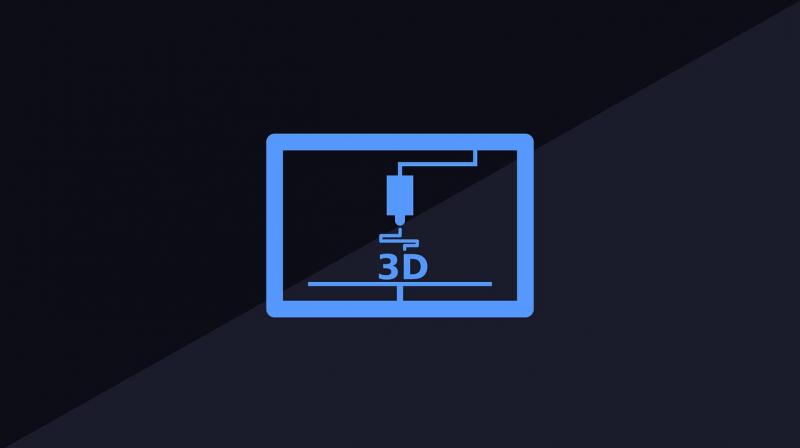
Three-dimensional printing, also called additive manufacturing, is a technique used to create solid shapes by building them layer by layer. It is now used in a wide range of applications, including manufacturing high precision parts like turbine blades, used in aerospace aircraft. Despite the high material cost, this technique is increasingly popular as the leap from digital design to a physical component is quick, involves fewer steps, is easy to customise, and a variety of materials can be used.
Simulations play an essential role in getting the manufacturing right the first time, and accurate numerical models form the backbone of simulations. Now, Prof Amitava De from the Indian Institute of Technology Bombay, and a team of researchers led by Dr Tarashankar DebRoy from Pennsylvania State University, USA, have developed a model to estimate the thermal and structural properties of components that are made using an additive manufacturing process called 'powder bed fusion'.
In the powder bed fusion method, components can be made from a wide variety of materials such as metals, ceramics and plastics. Hence, it is popular in medical and aerospace applications. It involves depositing a powdered alloy of metal in layers and melting specific areas using a laser beam to attain the desired shape. The structural properties, such as strength and hardness, of components, manufactured using this method, vary with the changes in the heat in different regions.
One could select the appropriate power of the laser beam, its scanning speed and strategy, the right size and distribution of the alloy powders and its composition, either by experimentation or by trial-and-error, to obtain the desired properties. However, this approach is costly, time-consuming and often unreliable. One solution to this problem is to understand the impact of these factors on the final structure and property of the fabricated part through fundamental mathematical models. Subsequently, based on the insights, a focussed set of experimentation must be carried out to optimize the final processing conditions. Previous studies by the same group of researchers have highlighted this approach. In this study, the researchers propose a numerical model in which the user can specify the operational parameters to obtain the desired properties of the final component.
A critical feature of the proposed model is that they have considered the mixing of hot metal by convection, which is closer to reality. As a result, these models provide more reliable results of thermal history and profiles of layer-by-layer 3D builds, in comparison to those models that consider only conduction of heat.
The model assigns appropriate values of thermal properties, such as thermal conductivity, to various regions of the component based on the heating, cooling and solidification of the metal alloy powder layer. It calculates the temperature distribution, the pressure and the flow velocity of the molten metal, which can then be used to predict the final structure of the component.
The temperature maps and the dimensions of the molten pool, computed by the numerical model, provides reliable values of temperature, cooling rates, and solidification parameters, which can then be used to control the process. For example, the size of the molten pool decreases with the increase in the speed of the laser movement. Therefore, a fast-moving laser will result in a small and quickly solidifying deposition that may be beneficial in 3D printing of parts with very intricate designs. Likewise, aluminium alloy attains the lowest temperature under the same settings because it diffuses heat very fast. In contrast, stainless steel with low thermal diffusion capability can achieve very high temperatures.
The researchers used the model to investigate the powder bed fusion process for four commonly used alloys of steel, titanium, nickel, and aluminium. These alloys behave differently under similar thermal conditions, and the model can capture this variation in its prediction. The aluminium alloy has the largest molten pool among the four under the same operating conditions owing to its low density and liquidus temperature—the temperature at which it is entirely liquid. This property helps in better fusion with subsequent layers of the metal. Since the stainless steel alloy has the smallest molten pool, the space between successive lines of laser movement has to be decreased to ensure proper fusion, which increases the time taken to build the component.
The substrate over which the powder layers are deposited conducts heat better than the powder. As it steals the heat from the first layer, the molten metal pool is smaller. As more layers are added, the distance of the substrate from the layers increases, decreasing the share of heat absorbed by the substrate and increasing the size of the molten metal pool. For alloys like aluminium which can pass heat faster to the layers at the top, this means that the fusion is better across the structure while for stainless steel with low diffusion capability, the fusion will be weaker.
As the laser moves line-by-line over each layer of powder, some heat is absorbed by the molten metal on one side, resulting in lesser heating of the powder and a smaller molten mass for succeeding lines in a layer. The speed and the space between each line of laser movement have to be adjusted to ensure that the molten metal fuses well with the previously melted layer.
The proposed model can thus provide accurate parameters for 3D printing for different alloys without the need for trial and error. It could also offer a comprehensive view of the manufacturing process and help produce high-quality components.