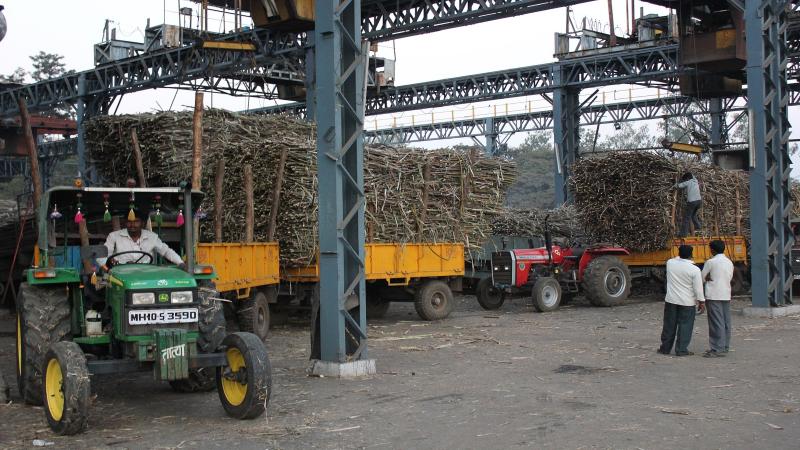
Image: Sugarmill in Maharashtra, India (Source: Wikimedia Commons)
Indians were among the first people on Earth, along with the indigenous people of New Guinea, to cultivate sugarcane and develop techniques to produce sugar from it. Over the years, newer processes have been developed to extract maximum juice from the cane and make sugar production profitable for the farmers and the sugar mills. However, despite India being the second-largest producer of sugarcane globally, farmers and sugar mills in India face substantial economic loss. The price of sugar in the country has remained relatively low, as the production is more than the demand. Export is not always sustainable as global sugar prices are often low.
One of the ways to mitigate the losses for the farmers and make sugar mills economically viable is to use sugarcane waste such as bagasse to produce value-added products. Bagasse is used as animal feed, to generate power or to make ethanol. They are making other biochemicals such as enzymes, lactic acid, or organic acids that can provide attractive avenues for revenue. However, developing economically viable processes in this regard remains a challenge.
Researchers from the Department of Chemical Engineering, Indian Institute of Technology Bombay and the Department of Alcohol Technology and Biofuels, Vasantdada Sugar Institute, Pune, recently studied how technically and economically viable it is to make lactic acid from sugarcane bagasse. They also studied the environmental impact of the production process. They found that a lactic acid production facility attached to a sugar mill can have significant economic and environmental benefits.
A small fraction of the total lactic acid produced globally, is currently produced by fermentation of sugars using lactic acid bacteria such as Lactobacillus or filamentous fungi. Over the years, researchers have tried to improve the efficiency of lactic acid production and make it cost-effective.
“Lactic acid has a fairly large market size in terms of quantity and value (500,000 tons/year; $ 2.9 Billion). It is used in pharmaceutical, food, cosmetic and polymer industries,” said Prof Yogendra Shastri, Associate Professor, Department of Chemical Engineering, IIT Bombay and a co-author of this paper.
However, not much importance is given to the environmental impact of the processes. Factors such as pre-treatment conditions, including loading of bagasse, process conditions and method of purification, affect both the economic and environmental performance of lactic acid production, and the outcome is specific to the region under study.
Vasantdada Sugar Institute (VSI) recently developed a new process to make lactic acid from bagasse at laboratory scale. The process includes four stages: pre-treatment, hydrolysis, fermentation and separation or purification. The pre-treatment of the bagasse is done using sodium hydroxide; the treated bagasse is then hydrolysed with the help of hydrolytic enzymes. The dissolved fraction from this step is used as a raw material for bacterial fermentation to produce lactic acid. Excess calcium carbonate is added into the fermentation broth to lower its acidity and extract lactic acid in the form of calcium lactate which is further purified to produce 99.9% lactic acid. The process also produces gypsum as a by-product, which finds application in the cement industry.
In the current study, the researchers carried out a techno-economic and Life Cycle Assessment (LCA) to understand the environmental impact of this new process at a commercial scale in India. The methodology stipulated by ISO 14040 included defining the goal and scope, analysing inventory and assessing the environmental impact of raw materials, transportation and product output, and interpreting the results. They assumed the commercial plant to be attached to an existing sugar mill in Maharashtra, considering optimal economic benefits.
The researchers used a combination of experimental data generated at the Vasantdada Sugar Institute (VSI) for the first three stages of the process from pre-treatment to fermentation, while they simulated the rest of the processes for purification of lactic acid on the ASPEN® analyser by feeding in the process parameters such as acidity, the quantity of bagasse, temperature among others.
The researchers found that the process generated 4.62 kg CO2 equivalent per kg of Lactic Acid produced, which is about 50% higher than emissions from using 1 liter of petrol. The major contributors to the emissions were the pre-treatment and hydrolysis steps. The production of sodium hydroxide used in the pre-treatment contributed to more than 50% of the total climate change impact. Similarly, the researchers also found that the total production cost was mainly affected by the variable costs including raw materials and utilities. Pre-treatment and hydrolysis were also the major contributors to the cost, together contributing to more than 80% of the costs due to the use of sodium hydroxide and enzymes in these steps. The techno-economic assessment also found that the lactic acid production process would turn profitable after six years at the prevailing market prices.
Since laboratory experiments and simulations are done in an ideal and controlled environment, the researchers expect real-world results to be different from those in the lab. “Disturbances and fluctuations in the process inputs are common. Therefore, one can expect the yields to go down, thereby negatively affecting the economics,” Prof Shastri claimed. However, commercial production plants offer many advantages, including automated process controls, better process equipment, and improved process efficiencies. “Overall, we claim that real-world costs could be ±25% of the values we have calculated,” he added.
These results helped the researchers to identify opportunities for improving the process. They found that more than 50% reduction in the cost and the climate change impact could be achieved by recycling sodium hydroxide, increasing the processing rate by loading more bagasse and reducing the usage of enzymes.
As the world adopts circular economy principles, it is essential to identify opportunities to develop economically viable processes for waste utilisation. It is also pertinent that these new processes reduce the negative impact on the environment. In this regard, a biorefinery that utilises every component in the product chain to create value is one of the ways forward.
This article has been run past the researchers, whose work is covered, to ensure accuracy.