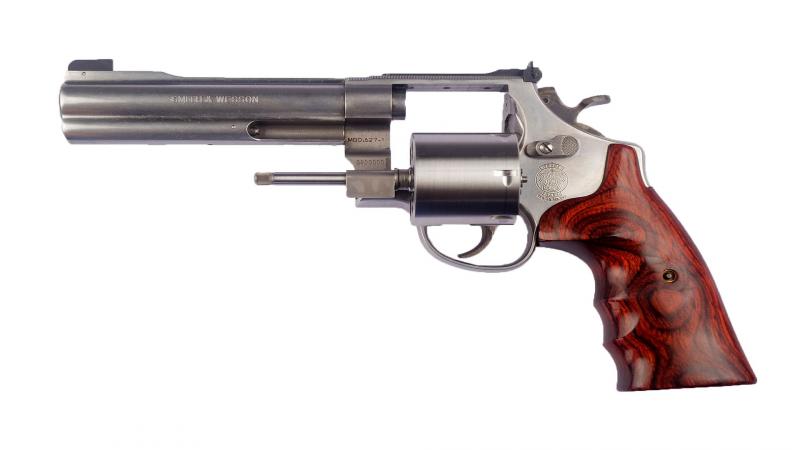
Every time a bullet is fired, it scrapes away a bit of the material from inside the gun’s barrel. Over time, the size of the barrel increases. Not only does this call for frequent maintenance, but could also lead to mistakes in hitting the target. The inside of the barrel is coated with protective materials such as chromium to avoid wear and erosion. Chromium (VI)—the hexavalent form of chromium—is popularly used as an electrolyte for coating deposition since it’s readily available and easy to use. But, it is carcinogenic and is also susceptible to cracking and falling off.
The trivalent form of chromium—chromium (III)—is as an environment-friendly and safer alternative. In a recent study, researchers from the Indian Institute of Technology Kanpur have explored the use of a new blend of chromium (III) as an eco-friendly electrolyte for depositing chromium-based coatings on metallic barrels. They reinforced chromium with carbon nanotubes (CNTs) and a ceramic compound called yttria stabilised zirconia (YSZ), to improve the properties of the coat. The Council of Scientific and Industrial Research, MHRD and Swarnajayanti Fellowship funded the study.
Usually, the barrels are coated using the electrodeposition process in which the barrel is submerged in an electrolyte solution containing the dissolved coating material. When an electric current is applied to the barrel, the dissolved particles are activated, and they uniformly deposit on its surface.
“Due to the complicated chemistry involved in the process, it is difficult to obtain very thick coatings of trivalent chromium compared to hexavalent chromium plating,” says Dr Kantesh Balani, who led the current study. “Incorporating carbon nanotubes make it more resistant to wear, and YSZ reinforcement gives it strength, so we obtain better coatings even at low thickness,” adds Pragya Shukla, who participated in the study.
The researchers analysed the properties of four different combinations of coatings on a flat steel plate—only chromium, chromium with CNTs, chromium with YSZ, and chromium with both CNT and YSZ.
Since YSZ is a non-conductor, the conductivity of the coating solution decreases, resulting in a thin layer of chromium and YSZ. In contrast, carbon nanotubes are conductors and increase the conductivity of the solution, forming a thicker layer of chromium and carbon nanotubes about twice the thickness of the chromium and YSZ coating.
Specific mechanical properties of the coating improved due to the additives. The researchers observed an increase in hardness of the coating and its resistance to wear. The chrome layer with both carbon nanotubes and YSZ was the hardest and most resistant to wear, indicating that it is least likely to erode. Moreover, when they scratched the surface with a steel ball, they found that there was less wear in the coatings containing carbon nanotubes than in the ones that did not. They attribute this to the lubrication provided by the carbon nanotubes.
The lowest wear in the coating with both carbon nanotubes and YSZ, report the researchers, highlighting the combined effect of the two additives. The zirconia strengthens the coat and reduces the propagation of cracks while carbon nanotubes lubricate and also fill up any cracks that might develop.
Using this new mixture instead of chromium (VI) would only need replacing the coating solution currently used in the industry. The suggested change is compliant with the current processes and would not require significant investments for its implementation.
“There will be a minor increase in cost due to the use of carbon nanotubes and YSZ. But, it would incur much lower costs than for other plating processes both in terms of investment and operating costs including labour costs,” says Shikha, a co-author of this study. “Besides, an enhanced life of the gun barrels may mandate the use of these coatings for ensuring the safety and longevity of barrels.” adds Dr. J. Ramkumar, another member of the team that carried out the study.
In the future, the researchers plan to test this coating on curved surfaces and with varying concentrations of carbon nanotubes and YSZ.
The researchers envision this plating process to be useful for not just gun barrels, but also hydraulic cylinders and rods, pistons for internal combustion engines and cutting tools.
“It can also be used in rebuilding worn parts such as rolls, moulding dies, cylinder liners and crankshafts,” signs off Dr Balani.
This article has been run past the researchers, whose work is covered, to ensure accuracy.