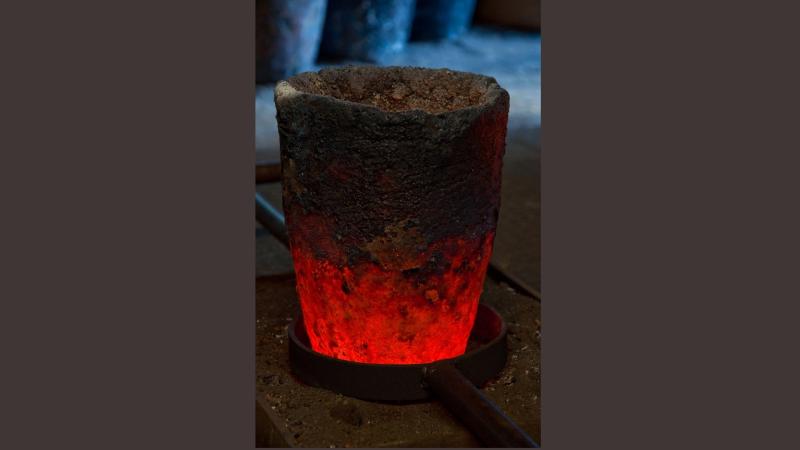
Iron Age finds from Tamil Nadu of some 2500 years ago reveal a great mastery of bronze metallurgy and the pioneering art of crucible steel making.
The southern Indian Iron Age, especially in Tamil Nadu, dating back to over 2500 years ago, has excelled in world-class metallurgy. As a testimonial to the then thriving metallurgical practices, various excavations since the late 1800s have unearthed classical Iron Age artefacts from peninsular India, including animal motifs, metallic objects, bronze vessels, iron weapons and ceramics. The famous ‘Damascus sword’ was a product of the Indian crucible steel making processes and was forged of special, high-carbon steel mainly made in southern India. Such Indian iron and steel traditions have found significant mention in the Greek, Persian and Roman records, dating back to the earlier part of the first millennium BCE.
In recently published, two-volume issues on Ancient Metallurgy by the journal Materials and Manufacturing Processes, Prof. Sharada Srinivasan from the National Institute of Advanced Studies (NIAS), Bengaluru, has documented some astounding facts about India’s ancient metallurgical processes.
In one of her papers, Prof. Srinivasan has uncovered the use of sophisticated high-tin bronze metallurgy in the Iron Age finds from Adichanallur, Tamil Nadu through scientific analysis. The excavations, which are now in the Government Museum, Chennai, are ranked amongst the earliest and finest examples of such metallurgy. Remarkably, the findings represent a continuing tradition from prehistory into recent times in Kerala. Unfortunately, many of these marginalised communities have also been affected in the recent Kerala floods. In the other paper, she points to evidence for skilled production of high-carbon steel by crucible processes from Mel Siruvalur in South Arcot district of Tamil Nadu.
Metallic objects are known to have unique structural properties at the microscopic level as a consequence of the processes in which they are made. Analysing metals at such micro-structural levels using electron microscopic techniques could reveal their composition and how they were forged. In the paper on Iron Age finds from Adichanallur, Prof. Srinivasan studied some very finely wrought vessels (broadly dated to the mid to early 1st millennium BCE) with intricate perforated designs and found microstructural evidence that they were made of heavily hot-forged high-tin beta bronze. ‘Beta’ phase in metallurgy is an intermetallic compound of copper and tin which forms at high temperatures, and high-tin beta bronze refers to an alloy of around 23% tin, which retains the beta phase. Such composition can be forged to a considerable degree at high temperatures, followed by quenching and it improves the tensile strength and tonality of the bronze.
“What is remarkable about some of these Adichanallur vessels is that they were extensively forged to a remarkable degree exploiting these properties of less than a millimetre rim thickness. Some were decorated with fine perforations showing extraordinary skill in working high-tin bronze and are fairly unique or rare early finds in that respect even in the world”, remarked Prof. Srinivasan in an interview with Research Matters. These highly wrought and perforated high-tin bronze vessels represent unique finds not found elsewhere in the world. She also documented rare surviving traditions in Kerala of this craft which has declined considerably over the years.
In another study on Wootz steel crucibles from Mel Siruvalur, South Arcot, Tamil Nadu, Prof. Srinivasan has uniquely reported concrete evidence for crucible carburisation of wrought iron to high carbon steel. This finding correlates to the 19th century descriptions from the Tamil region and also finds echoes in the Greek accounts of Zozimus of the 2nd century BCE. The ultra-high carbon Wootz steel was the material used for making the Damascus swords exported to West Asia. She also points out that the word Wootz comes from the ‘ukku’, which is derived from the Tamil word ‘urukku’ meaning ‘melting in a vessel’. The metallic properties and the alloy constituents of these antiques have intrigued scientists from all over the world, including Michael Faraday who studied specimens of Wootz.
Further investigations on the crucible fragments of Mel Siruvalur have shown that these crucibles are made of ‘hypereutectoid’ or ultra-high carbon steel. Steel, an alloy of iron, has small amounts of carbon added to it, and regular steel usually has 0.4% carbon. However, hypereutectoid steel refers to an alloy with about 1.5 to 2% carbon. Such high-carbon steel could be made by a method called carburization where carbon is gradually added to iron to make it steel, the study believes.
The high carbon content in crucible steel such as the traditional Wootz steel could be achieved by packing the iron blooms with carbonaceous materials and firing the furnace at high temperatures not less than 1400°C for a long time. This process is known as the crucible steel process. Observations from the 19th-century travellers described the existence of three such crucible processes in southern India—the Deccani or Hyderabadi process, the Mysore process and the Tamil Nadu process. Out of these three, the Tamil Nadu process is noted to be unique and considered to be the oldest of all.
“The Tamil Nadu process seems to be an older route to make crucible steel since it correlates to the description of the Greek Zosimus of Indians making metal for spears in crucibles. Other processes may have developed out of that eventually. What was noticeable at Mel Siruvalur was that the crucible remnants showed that the end product was homogenous hypereutectoid steel. This steel was made of the kind which could have been forged and etched to get the well wavy light and dark patterns of the wootz or Damascus steel blade, which was much sought after in Persia and the Arab world”, explained Prof. Srinivasan.
However, the past glory of this metallurgical expertise could soon vanish due to our inaction, warned Prof. Srinivasan. “The recent floods have had an impact on several craftspeople as well who live near the riverbanks such as high-tin bronze workers who live along the Bharatapuzha river and the metal mirror makers of Aranmula who need to be rehabilitated. The findings also highlight the pressing importance of documenting and preserving metallurgical heritage, which is also susceptible, especially in the case of bronze vessels, to recycling, remelting and reuse and hence, to getting lost to posterity. Sometimes vessels don’t capture the imagination like icons and are not well preserved or inventoried. The archaeo-metallurgical landscapes of slag mounds and crucible heaps which were production centres in antiquity have also not been well preserved and are vulnerable to being obliterated to make way for agriculture, roads, filling ditches and such like”, she said.
Studies such as these throw significant light on the skilled technological traditions of southern India and stand testimony to the mastery and great sophistication of metallurgy during the Iron Age that is generally unrecognised. These findings strongly emphasise the need for archaeological studies and preservation of megalithic and Iron Age sites which have historical importance. “There has to be more awareness of the need to also preserve such aspects of scientific and technological heritage for posterity. There is also a need to foster more interest in the disciplinary study of scientific archaeology”, signed off Prof. Srinivasan.