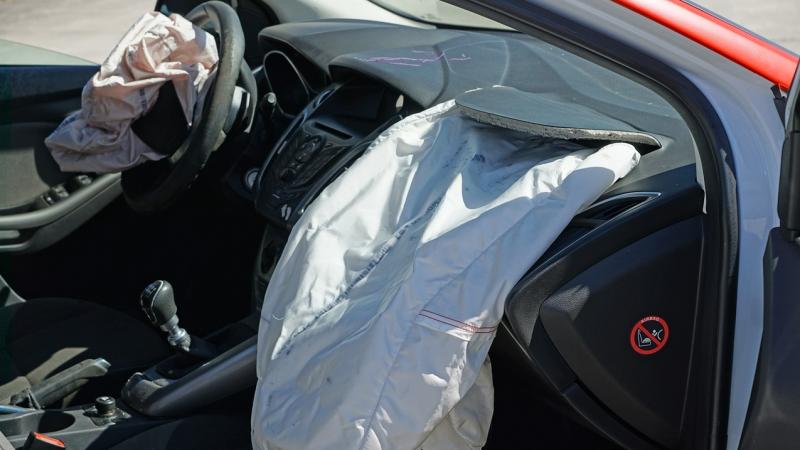
Airbags in vehicles are a mandatory safety feature today. The idea of an airbag is that in an unfortunate event of a crash, it inflates and protects the passengers from the direct impact of a collision. But, how does the airbag know when to expand? A tiny 'crash sensor', placed in the automobile, detects the collision and sends a signal to inflate the airbags, unlock the doors or make an emergency call. An ideal crash sensor should recognise the magnitude of a crash, respond very quickly and mitigate adversities. In a recent study, researchers at the Indian Institute of Science, Bengaluru, have designed such a crash sensor using zinc oxide (ZnO) thin films.
Recent advances in technology have resulted in the fabrication of sensors that use the piezoelectric effect—the conversion of mechanical input into electrical output. These sensors are energy efficient, compact, and can be custom-built to suit different applications. In the current study, published in the journal Small, the researchers have designed and tested a zinc oxide-based piezoelectric sensor that can detect crash events, differentiate the crash occurring with a hard or a soft target, and respond within 18 milliseconds—a duration much lesser than what it takes to blink our eyes.
“In the future, automated vehicles will be driverless and hence will rely heavily on smart sensors for navigation and passenger safety. We believe that our miniaturised, thin-film crash sensor with faster response time is a step towards realising smart sensing in next-generation vehicles”, says Dr. Sudeep Joshi from IISc, who is an author of the study.
The researchers developed the sensor by depositing a 700-nanometer thin film of zinc oxide onto a highly flexible substrate called Phynox—a metal alloy of cobalt, chromium and nickel. They optimised the process parameters for the fabrication of the zinc oxide layer to obtain highly-crystalline, vertically-aligned nanostructured ZnO with an enhanced piezoelectric property. This layer is then sandwiched between a thin film of gold and Phynox, which act as electrodes. The sensing element is a cantilever, with one flexible end to bend and vibrate.
“Our group at IISc holds a decade of expertise and experience in depositing high-quality piezoelectric ZnO thin films. We have well-established process parameters which result in repeatable and reproducible piezoelectric thin films on a wide variety of substrates”, mentions Dr. Joshi on their expertise in the fabrication process.
The researchers tested the sensor by attaching the cantilever to the front hood of a remote-controlled car and allowed it to collide with a target. They then analysed the different impact forces and electrical outputs signals generated when it crashed with a hard target (an iron plate) and a soft target (styrofoam), at different speeds.
When the remote-controlled car collides with the target, a load cell attached to the target displays the force it exerts on the vehicle at the time of the collision. When the car crashes with the iron plate, it results in an elastic collision, where the car and the target are not in contact with each other after the crash. The vehicle also moves a certain distance in the reverse direction after hitting the target. In the case of styrofoam, it results in an inelastic collision, where the car and the target remain in contact with each other after the crash. The soft target provides some cushioning effect that slightly reduces the magnitude of the impact force. The newly developed sensor could remarkably differentiate between the two types of crash events.
So, how exactly does the sensor work? As soon as the car collides with the target, the cantilever bends, vibrates and experiences mechanical stress. Due to the vibrations, the charge distribution in the piezoelectric zinc oxide film gets affected. Positive and negative charges get accumulated on the film, setting up a potential difference, and resulting in the flow of electrons between the two electrodes. An oscilloscope displays the electrical voltage output given by the piezoelectric sensor at the time of the crash. As the initial speed of the car increases, the vibration of the cantilever after collision also increases, leading to an increase in the amplitude of the output voltage generated by the sensor.
As part of the future research, the researchers plan to analyse the performance of the crash sensor in field-testing studies. “We are in the process of discussion with researchers and industrial experts for the next step towards integrating the thin film sensor with vehicles to obtain real-time data for crash studies.” , signs off Dr. Joshi.